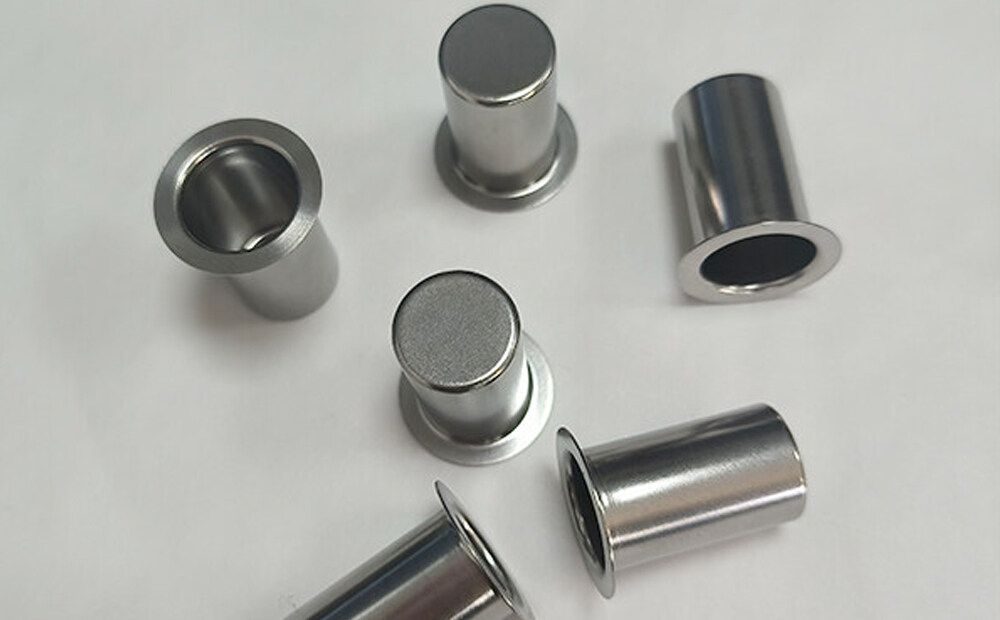
不同類型的拉伸件模具在結(jié)構(gòu)、工藝等方面存在差異,以下是幾種常見拉伸件模具在預(yù)防問題方面的特殊考慮:
圓筒形拉伸模具
防止起皺:由于圓筒形拉伸件在拉伸過程中,坯料的邊緣容易出現(xiàn)起皺現(xiàn)象,所以要特別注意壓邊力的控制。壓邊力過小,無法有效抑制起皺;壓邊力過大,則可能導(dǎo)致坯料破裂。可采用可變壓邊力技術(shù),在拉伸初期施加較小的壓邊力,隨著拉伸的進(jìn)行逐漸增大壓邊力,以更好地控制起皺。
控制壁厚均勻性:模具的凸凹模間隙均勻性對圓筒形拉伸件的壁厚均勻性影響很大。在模具制造過程中,要嚴(yán)格保證凸凹模的同軸度,采用高精度的加工設(shè)備和測量儀器,確保間隙偏差控制在較小范圍內(nèi)。例如,使用數(shù)控加工中心進(jìn)行加工,通過精確的編程和加工工藝,保證凸凹模的尺寸精度和同軸度。
優(yōu)化潤滑條件:為了減少坯料與模具之間的摩擦,降低拉伸力,防止拉毛和破裂,良好的潤滑至關(guān)重要。選擇合適的潤滑劑,如含有極壓添加劑的潤滑油,并采用合理的潤滑方式,如在模具表面均勻噴涂潤滑劑,或在坯料表面涂抹潤滑脂等。
盒形拉伸模具
角部處理:盒形拉伸件的角部是應(yīng)力集中的部位,容易出現(xiàn)破裂或起皺。在模具設(shè)計時,要合理設(shè)計角部的圓角半徑,一般來說,角部圓角半徑應(yīng)根據(jù)拉伸件的材料、厚度和尺寸等因素來確定,通常取 3 - 5 倍的材料厚度。同時,可在角部設(shè)置加強(qiáng)筋或過渡圓角,以改善應(yīng)力分布,降低角部的應(yīng)力集中。
非均勻間隙設(shè)計:由于盒形拉伸件在拉伸過程中,不同部位的變形程度不同,因此模具的凸凹模間隙應(yīng)采用非均勻設(shè)計。在角部區(qū)域,間隙可適當(dāng)減小,以增加材料的流動阻力,防止角部破裂;在直邊區(qū)域,間隙可適當(dāng)增大,以利于材料的流動,避免起皺。
坯料形狀優(yōu)化:盒形拉伸件的坯料形狀對拉伸質(zhì)量有重要影響。根據(jù)盒形件的尺寸和形狀特點(diǎn),采用合理的坯料形狀,如采用橢圓形或梯形坯料,可使材料在拉伸過程中更加均勻地流動,減少起皺和破裂的可能性。
復(fù)雜形狀拉伸模具
多步拉伸與過渡設(shè)計:復(fù)雜形狀拉伸件通常需要采用多步拉伸工藝,在模具設(shè)計時,要合理規(guī)劃每一步的拉伸形狀和尺寸,設(shè)計好過渡形狀,使材料在拉伸過程中逐步變形,避免一次拉伸變形過大導(dǎo)致的問題。例如,對于具有不規(guī)則形狀和深度變化的拉伸件,可采用漸進(jìn)式拉伸模具,通過多個工位逐步完成拉伸過程。
局部結(jié)構(gòu)強(qiáng)化:針對復(fù)雜形狀拉伸件的局部復(fù)雜結(jié)構(gòu),如凸起、凹陷、翻邊等,在模具設(shè)計時要對相應(yīng)部位進(jìn)行結(jié)構(gòu)強(qiáng)化。例如,增加模具的支撐結(jié)構(gòu),提高模具在這些部位的強(qiáng)度和剛度,防止在拉伸過程中因局部受力過大而導(dǎo)致模具變形或損壞。
采用先進(jìn)制造技術(shù):復(fù)雜形狀拉伸模具的制造難度較大,可采用先進(jìn)的制造技術(shù),如電火花加工、激光加工、快速成型技術(shù)等,以提高模具的制造精度和表面質(zhì)量,保證模具的復(fù)雜結(jié)構(gòu)能夠準(zhǔn)確加工出來,減少因模具制造誤差導(dǎo)致的拉伸問題。
變薄拉伸模具
控制拉伸比:變薄拉伸的拉伸比直接影響拉伸件的質(zhì)量和模具的壽命。拉伸比過大,會使材料變薄過度,容易導(dǎo)致破裂;拉伸比過小,則無法達(dá)到預(yù)期的變薄效果。因此,要根據(jù)材料的性能和模具的承受能力,合理控制拉伸比,一般拉伸比在 1.5 - 2.5 之間為宜。
模具材料與表面處理:由于變薄拉伸過程中模具與材料之間的摩擦力較大,對模具的磨損較為嚴(yán)重,所以要選用耐磨性好、硬度高的模具材料,如硬質(zhì)合金等。同時,對模具表面進(jìn)行特殊的處理,如鍍硬鉻、金剛石涂層等,以提高模具表面的硬度和光潔度,降低摩擦系數(shù),減少模具的磨損。
精確控制工藝參數(shù):變薄拉伸對工藝參數(shù)的要求非常嚴(yán)格,需要精確控制拉伸速度、進(jìn)給量、潤滑條件等參數(shù)。拉伸速度過快,會使材料發(fā)熱嚴(yán)重,導(dǎo)致材料性能下降,容易出現(xiàn)破裂;進(jìn)給量過大,則會增加模具的負(fù)荷,影響模具壽命。